

It is also accompanied by a shielding gas that protects them from contaminants. Also known as MIG (Metal Inert Gas) welding, GMAW is a semi-automatic or fully automatic method that uses a continuous solid wire electrode (similar to the workpieces) to weld the workpieces together. This technique is the most common welding technique used in welding many materials. However, it produces strong and quality welded joints. TIG welding does not use flux, and it requires great precision. It involves using a tungsten electrode to melt the workpiece, creating a liquid pool that joins them on solidification. Gas Tungsten Arc Welding (GTAW)Īlso known as TIG (tungsten inert gas) welding, GTAW is suitable for ferrous or nonferrous metals such as stainless steel, aluminum, and titanium. Stick welding is a simple, portable, and inexpensive method suitable for welding ferrous materials such as low and high alloy steels, carbon steels, cast iron, and nickel alloy. The flux melts together with the electrode but forms gas and slag, which protect the molten electrode and the electric arc. The molten electrode fills the space between the two sheet metal parts to be joined.

SMAW or stick welding is a welding technique that involves using a flux-coated electrode connected to a power source to weld the sheet metal parts. Here are the popular methods: Shielded Metal Arc Welding (SMAW) There are many welding processes you can use to join two sheet metal parts together. It is a permanent process that involves aligning the metal, melting the metal parts, and cooling them to allow the parts to form rigid joints. Welding is a thermal process used in joining two similar or dissimilar metal parts. Corrosion can occur in the riveted area leading to an increase in maintenance cost.Disassembling does not lead to damaged riveted parts.It is easy to perform a quality inspection.More suitable for dissimilar and non-ferrous metal parts.Riveting is a non-heat metal joining method.Riveting is a popular joining method in most sheet metal fabrication services. Zig Zag Riveted Joint: Unlike the chain strap butt joint, the Zig Zag Riveted Joint’s rows of rivets don’t complement each other.Chain Riveted Joint: To form the chain riveted joints, ensure that rows of rivets are exactly opposite each other and in straight lines.This category focuses on the arrangement of the rivets you used in joining the sheet metal parts. Use two cover plates placed at the opposite side of the two sheet metal parts and rivet each cover plate.
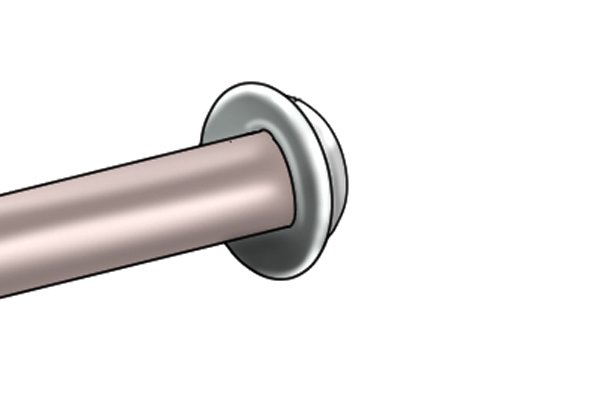
The only difference is that the two sides have a cover plate. Double Strap Butt Joint: This is like the single strap butt joint.Then place a cover plate on one side of the main plate and rivet it. Single Strap Butt Joint: To form a single strap butt joint, place the main plates against each other without overlapping.This category of riveted joints is for butt joints. You then rivet the cover plate.Ĭover plates are materials you place on the workpieces to hold them such that you can drill through them. Butt Joint: You can create a butt joint by butting up two components together (hence the name butt joints) and using additional material (a cover plate or strap) to bridge them either on one side or both sides.Lap joints can be single or double, depending on the number of rivets you use. Lap Joint: You can create a lap joint by overlapping the two sheet metal parts and installing a rivet on the overlapped portion.There are two types of riveted joints based on the placement: However, there are three main categories of riveted joints. Riveted joints are made by inserting a rivet into a drilled hole in the two sheet metal parts. Together with the shaped head, the flattened tail prevents the removal of the rivets. This is achievable by pounding or smashing it. Installation depends on the type of rivets you are working with, as you might have to place, drill, or punch the rivets into the hole.Īfter installing the rivets in the hole, you have to deform the rivet’s tail. Riveting involves drilling a hole in the two sheet metal parts you want to join together and installing a rivet. Riveting is a semi-permanent and non-thermal joining method that involves using a mechanical fastener/rivet (a metallic part with a dome-shaped head) to join sheet metal parts. This article further does justification to the definition, the pros and cons, and applications of welding and riveting that will help you get stronger and more durable parts. Therefore, if you’re designing a part that you need to join to form a complete object, it’s crucial to understand riveting vs welding comparison. Welding and riveting are broadly popular joining processes to fuse two pieces of metal together and they have different applications and traits.
